
Member Benefits, Programs, and ServicesAll our repairs meet the relevant manufacturer’s guidance and British Standards and include a 24-month workmanship guarantee. Step 2 - Taking Defective Areas Out If there are cracks or separation in the veneer bricks, take them out and replace them. Inspect the locations where the brick meets with mortar more carefully. This should include the head joints and vertical mortar. Inspect the surface of your exterior brick veneer wall for any obvious cracks.
Home Facade Repair For Free Consultation Today
Registered Exterior Wall Observer – REWO® Registered Exterior Wall Consultant – REWC® Mowla Home Improvement Recent Posts Registered Waterproofing Consultant – RWC®Brooklyn Facade Repair contractor, we specialized in kinds of Facade repair or replacement work, call us for free consultation today. Simple mortar repair could cost less, between 7 and 13 per square foot, while expensive stone replacements on the second or third floor of a home could cost significantly more, 60 to 100. SHOW SOLUTIONS.Exterior stone veneer repair costs for an average repair, such as replacing chipped, cracked, or buckling stone, will run from 20 to 60 per square foot.
2022 IIBEC International Convention and Trade Show 2021 IIBEC International Convention and Trade Show Certified Building Enclosure Commissioning Provider – CBECxP®

These ties consist of a steel plate connected to the steel stud backup, with a slotted connection protruding through the exterior sheathing to accommodate the wire tie, which is embedded in mortar ( Figure 1). Challenge 1: Lateral Support – Brick TiesSeveral original construction deficiencies related to the lateral support systems were uncovered during our initial investigation, including improperly installed and failed brick ties at steel stud backup walls and inconsistent brick tie spacing at cast-in-place concrete backup.Wall areas with steel stud backup were designed with wire-and-plate-style ties (also referred to as unit ties). The focus of this article will be on the design and implementation of repairs, including those related to concealed conditions. These challenges needed to be addressed in an environment of relative uncertainty, as is the case with existing buildings. For a variety of reasons—including escalating costs—the work was halted with only about 25% of the work complete.Among our challenges would be confirming the extent and sufficiency of repair work already completed, and developing and implementing an effective retrofit solution for the fa&cceil ade.
During our review, we discovered track spacing varying from 19 to 26 in. The dovetail ties are installed in vertical metal tracks that are cast into the wall structure. The dovetail tie spacing was inconsistent in both the horizontal and vertical directions. Figure 3 – Existing wire-and-plate brick tie failed connection to metal stud backup.At areas with cast-in-place concrete backup, dovetail-style brick ties were installed (Figure 4), but similar to the wire-and-plate ties, there were issues with the original installation. Furthermore, we uncovered disconnected plate connections at steel stud backups ( Figure 3) at 12% of interior test openings performed.Figure 2 – Improper installation at existing wire-and-plate brick tie at steel stud backup. The horizontal spacing is consistent with interior metal stud spacing.At over 50% of the locations reviewed, wire ties were installed backwards, relying only on the back-turned leg of the tie to provide lateral support ( Figure 2).
Figure 6 – New retrofit helical brick ties engaged at metal stud backup.Previous repairs were performed using a brick tie design requiring ten retrofit ties per stud (or per 16-in. Suitability of this application was established through pullout testing throughout the installation process to ensure adequate lateral support at the façade.Figure 5 – Pilot hole through a mortar joint and helical tie. A small mortar joint repair to conceal the tie completes the installation. These ties are installed by first pre-drilling a pilot hole through the mortar joint and backup ( Figure 5), then drilling the helical tie through the mortar joint and into the backup structure ( Figure 6).
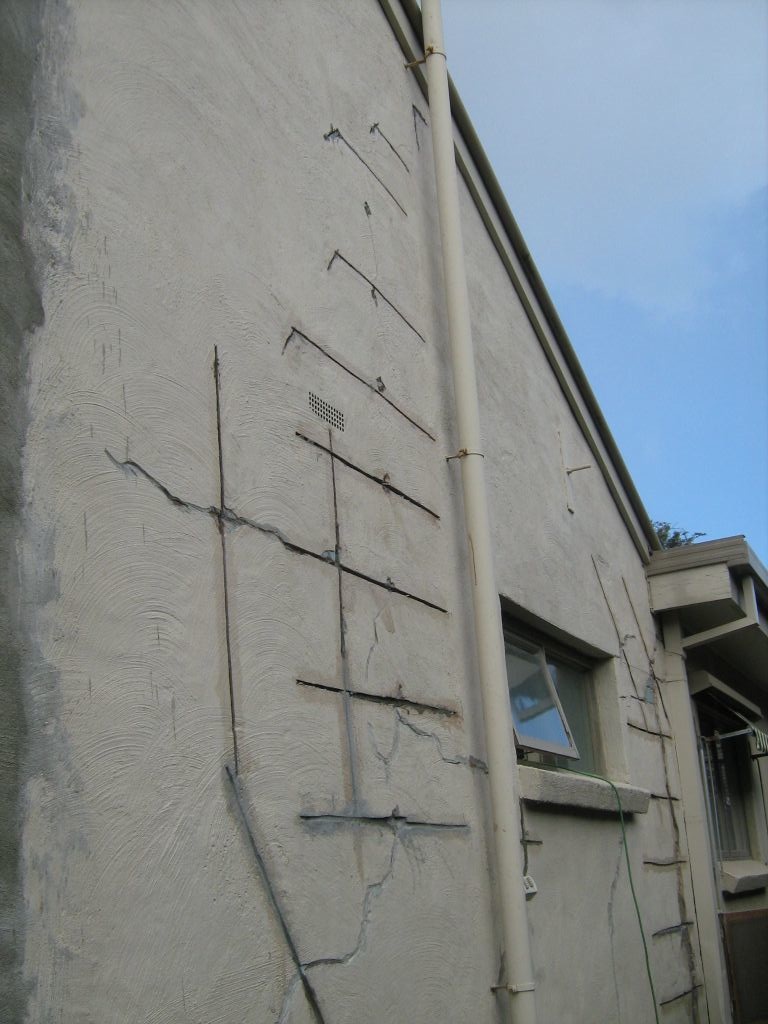
Home Facade Repair Full Exposure Of
Figure 8 – No support at existing shelf angle.We carried out structural analysis of the existing shelf angle systems and confirmed that two stories of masonry could be safely supported by one shelf angle. We observed some locations where the shelf angle was providing inadequate support, and some locations where the shelf angle was providing no support at all ( Figure 8).Figure 7 – Checking shelf angle overhang (1¾ in. Instead, we performed localized openings at shelf angle toes to measure overhang ( Figure 7). It’s important to note that the brick installation was an original construction defect, and that we did not observe major signs of structural distress that would indicate immediate safety concerns or risk of sudden movement.Full exposure of all shelf angles to check overhang would have been unduly costly. Of course, this use of mortar also facilitated load transfer to the shelf angles below, resulting in possible overloading concerns. In many areas, bricks had been installed beyond the toe of the shelf angle so far that the engineered joint was instead filled with mortar to provide support to the brick above.
Challenge 3: Shelf Angle SecurementDuring repair implementation, we uncovered a previously unforeseen condition related to shelf angle securement. Figure 10 – New through-wall flashing and brick reinstatement. Repaired shelf angles were then waterproofed, and bricks were reinstated ( Figure 10).Figure 9 – New shelf angle extension and reinforcing. Stiffener plate spacing was designed to accommodate existing brick coursing. Additionally, this change resulted in a proportional cost savings for the owner.Where repairs were required, shelf angles were extended and reinforced in place with welded steel extension and stiffener plates, custom-sized based on the repair location and existing overhang ( Figure 9).
Washer not making full contact due to oversized bolt slot. Ortunately, we were able to back off the existing nuts to provide a new, larger washer ( Figure 12).Figure 11 – Existing bolted shelf angle. These modifications required repair, since they resulted in bolt slots that were oversized or too close to the edges of the shelf angle.At areas with oversized bolt slots, the existing washers were not making full contact with the shelf angle around the bolt slots ( Figure 11). As a result, we did not expect to uncover these bolted connections while conducting repairs.Consistent with the workmanship from original building construction previously described, the shelf angles appeared to have been crudely modified on site during installation to accommodate bolt locations and masonry coursing. This method of shelf angle securement was not uncovered during the limited initial review, nor was it identified on the original construction drawings provided.
